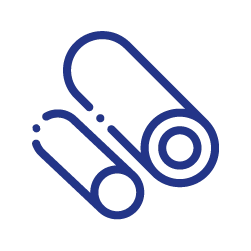
Pumps for the galvanic industry
The galvanic treatment sector requires highly specialised pumping solutions for the handling of aggressive fluids, such as acids, alkalis, galvanic solutions and electrolytes, used in metal coating and surface treatment processes. These processes require reliable and resistant pumps that guarantee precision, safety and durability even in critical operating conditions.
Fluimac offers a range of pumps designed specifically to meet the needs of electroplating, with corrosion-resistant materials and a design that allows a safe and continuous transfer of fluids. Fluimac pumps are ideal for the recirculation of galvanic solutions, the precise dosing of chemicals and the handling of liquids at high temperature or viscosity.
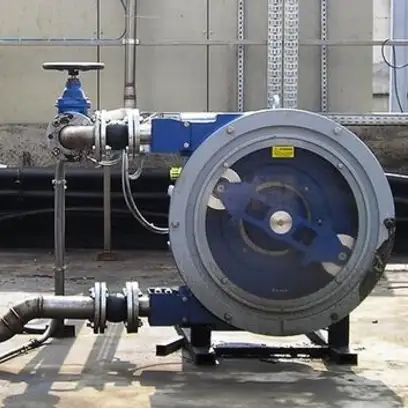
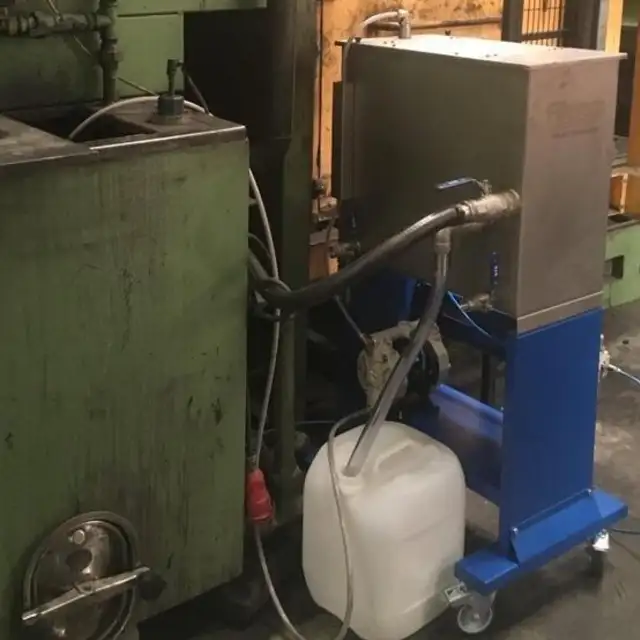
Use of Fluimac pumps in the galvanic sector
Operators in the galvanic sector are acutely aware of how important the surface treatment of metals is in ensuring superior strength, durability and finishes. In this kind of context, however, the transfer and handling of aggressive fluids, such as acids or corrosive chemicals, involves significant challenges and risks related to the safety, efficiency and longevity of the equipment used.
Years of experience and research aimed at the continuous improvement of the solutions proposed, make Fluimac corrosive liquid pumps the reliable, high-performance solution for the handling of liquids used in galvanic baths and surface coating processes. The Fluimac pump range, including Phoenix, Compass, Dragon and Neptune models, is designed to address the most complex needs of the galvanic industry.
Thanks to their chemical compatibility and the robustness of the construction materials, these pumps guarantee the safe handling of corrosive and viscous liquids, minimising operational risks and increasing the life of the systems. For example, in processes involving dosing systems, such as the dosing of chemical additives or the treatment of high-temperature fluids, and galvanic solutions, Fluimac models offer an uncompromising and outstanding performance.
A hallmark element of Fluimac pumps is, in fact, the possibility of configuring the construction materials according to the fluid being treated. Components made of PP, PVDF, PTFE, stainless steel, and other corrosion-resistant materials ensure full compatibility with even the most aggressive chemicals. This flexibility allows the pumps to be adapted to each specific application, such as galvanic bath treatments or the handling of chemical agents intended for the surface treatment of metals.
For operators in the galvanic sector, precision is essential. In addition to ensuring safe and precise handling of fluids, Fluimac pumps help to improve the overall efficiency of the production process, minimising waste and optimising the dosage of chemicals.
Benefits of using fluid-handling solutions for the galvanic sector
Since the galvanic industry requires equipment capable of guaranteeing reliability and safety in the handling of complex fluids, Fluimac pumps are the ideal solution to face the challenges related to this sector, offering a unique combination of versatility, durability and competitiveness. In practical terms, opting for Fluimac has several benefits, including both safety and savings.
With Fluimac, you get:
- Resistance and service life
One of the main benefits of Fluimac pumps is their resistance to corrosion, obtained through the use of high-performance materials such as PP, PVDF, PTFE and stainless steel. These materials increase strength and guarantee not only a long service life, but also excellent chemical compatibility with aggressive, acidic and alkaline fluids, commonly used in galvanic treatments. In addition, Viton or EPDM seals further improve reliability, preventing leaks and ensuring optimal sealing even in extreme conditions.
- Optimisation of the galvanic production process
The handling of viscous fluids and high temperatures poses an additional challenge that has been successfully overcome by Fluimac centrifugal pump models. Their ability to accurately dose chemical additives and agents intended for metal surface treatments allows for uniform coatings and superior quality in the final products. This translates into greater competitiveness for companies in the galvanic sector, which can rely on reliable and high-performance solutions to optimise their production processes.
- Dedicated and tailor-made technical support
Another strength of Fluimac pumps is the dedicated technical support service. The Fluimac team offers highly qualified support for the selection of the most suitable materials and configurations for each application, ensuring a service tailored to the needs of customers. This technical expertise is particularly appreciated in a complex sector such as electroplating, where every detail can make a difference.
Fluimac pumps have established themselves as a benchmark in the galvanic sector, thanks to their ability to combine reliability, efficiency and innovation. Whether handling corrosive fluids, dosing chemical additives or handling viscous and high-temperature fluids, these solutions stand out for their excellent performance and ability to respond to specific market needs. Choosing Fluimac means investing in safety, durability and expertise, ensuring tangible added value for each stage of the galvanic process.
Thanks to their cutting-edge design and ability to respond to the most demanding requests, Fluimac pumps offer a strategic solution for the treatment of aggressive fluids and optimisation of galvanic baths.
To find out about all the details for the available models and their applications, or to receive a free consultation: Contact us now to speak with one of our experts.
Fluimac pumps for the galvanic industry
Fluimac offers a range of pumps designed specifically to meet the challenges of the galvanic industry.
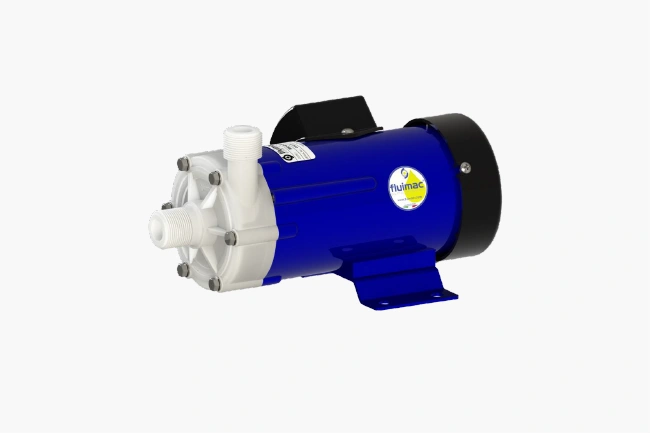
Fluimac’s Compass magnetic drive centrifugal pumps are the ideal choice for the galvanic sector, where the handling of highly corrosive and aggressive fluids, such as acids, alkalis and galvanic solutions, requires maximum safety and reliability.
Thanks to the hermetic design, free of mechanical seals, Compass pumps eliminate the risk of leaks, ensuring a safe and continuous transfer of fluids. Made of highly resistant materials such as PP and PVDF, they offer excellent chemical compatibility, ensuring long-lasting performance even in critical environments.
- Superior chemical resistance: compatible with galvanic solutions, electrolytes and aggressive chemicals.
- Operational safety: magnetic drive prevents leaks and contamination, ensuring safe working environments.
- Efficiency in recirculation and transfer: designed to maintain a constant flow in the anodising, chrome- and nickel-plating processes.
- Reduction of maintenance costs: the modular design minimises component wear, optimising operating life.
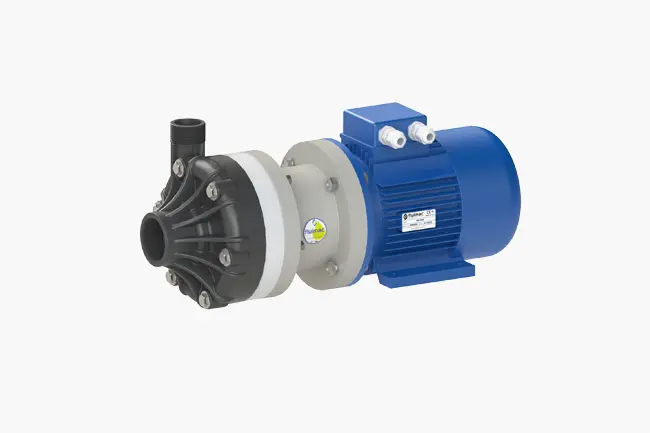
Fluimac’s Dragon centrifugal pumps with mechanical seal are designed to meet the specific needs of the galvanic sector, ensuring efficiency and durability in the handling of aggressive fluids such as acids, alkalis and galvanic solutions used in metal surface treatments.
Thanks to the robust construction and semi-open impeller, Dragon pumps effectively handle abrasive and chemically complex fluids, ensuring consistent performance even in demanding work environments. The virgin PTFE mechanical seal offers corrosion resistance and optimal protection against leaks and contamination, making these pumps the ideal reliable and durable solution for optimising galvanic processes, improving productivity and ensuring operational safety.
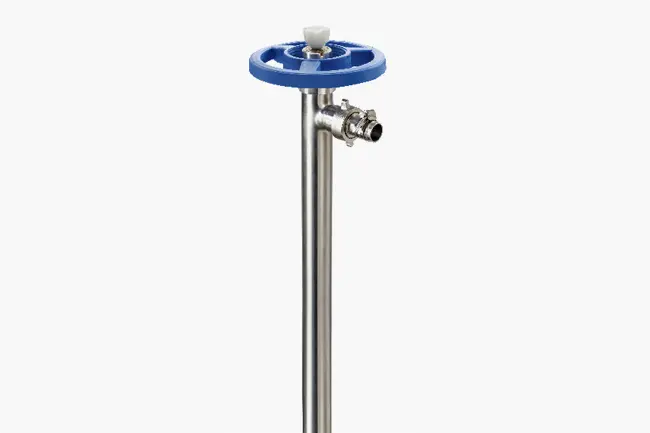
Fluimac’s Neptune drum transfer pumps are designed to address the needs of the galvanic sector, ensuring the safe and precise transfer of aggressive fluids such as acids, alkalis, galvanic solutions and other chemicals used in metal surface treatments.
Thanks to their modular structure and the possibility of customising the materials in contact with the fluid, Neptune pumps ensure high chemical compatibility and optimal fluid management in critical applications.
Neptune pumps are the ideal solution to ensure efficiency and safety in the galvanic sector, improving fluid transfer processes and optimising productivity.
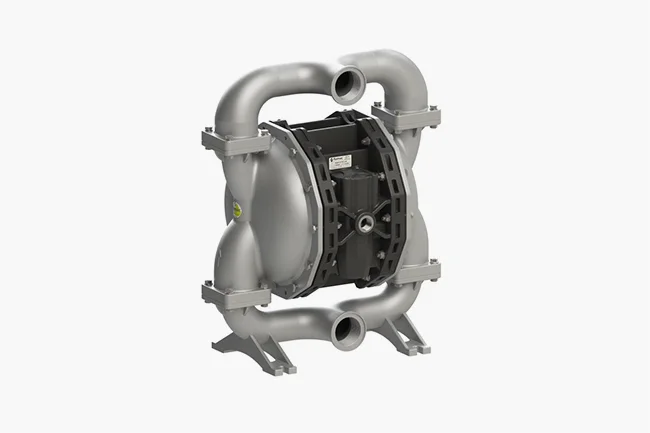
Fluimac’s Phoenix diaphragm pumps are an excellent solution for the galvanic sector, where the handling of aggressive fluids such as acids, alkalis, galvanic solutions and electrolytes requires reliability, precision and chemical resistance.
Designed with high-quality materials such as PP, PVDF, PTFE and AISI 316 steel, Phoenix pumps offer superior chemical compatibility and safe operation even in critical environments. The dual diaphragm design allows for the handling of abrasive or solid particle fluids, ensuring consistent performance and long life.
Applications
- Recirculation of galvanic solutions
- Galvanic bath feed
- Dosage of chemical additives
- Neutralisation and pH regulation
- Tank filling and emptying
- Transfer of acidic and alkaline fluids
- Wastewater management
- Surface treatment system feed
- Emptying of tanks and vessels
Reasons for choosing Fluimac
High-quality materials
Fluimac pumps are made of highly resistant materials, such as PP, PVDF, PTFE and AISI 316 steel, designed to handle chemically aggressive fluids, such as acids, alkalis and galvanic solutions. These materials guarantee long life and optimal protection against corrosion, meeting the specific needs of the galvanic sector.Safety and reliability
Designed to offer maximum safety in the handling of corrosive fluids, Fluimac pumps prevent leaks and contamination, helping to maintain the efficiency and quality of galvanic processes.Precision dosing
Fluimac pumps ensure the precision dosing of electrolytes, chemical additives and treatment solutions, ensuring accurate control at every stage of the anodising, chrome- and nickel-plating processes.Efficiency and speed
Our solutions are designed to operate continuously, with a constant and reliable flow, optimising the transfer and recirculation of galvanic fluids. Their ease of installation and maintenance reduces downtime and operating costs.Resistance and care in handling
Fluimac pumps are able to handle abrasive fluids and solid particles in suspension, preserving the chemical and physical properties of the solutions used in galvanic processes.Request a consultation
Do you need help in choosing the best pump for your specific fluid handling needs?
Fill in the form below and you will be contacted by our staff.
The best solutions, certified
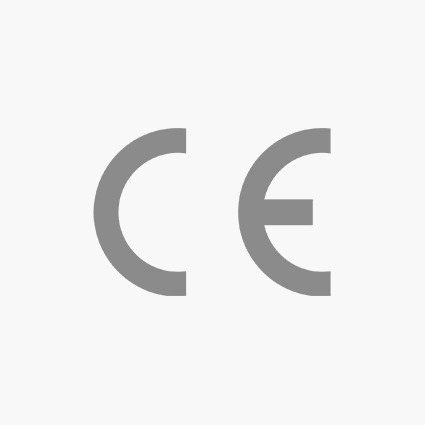
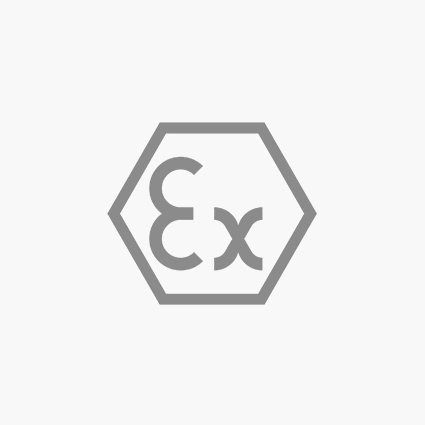
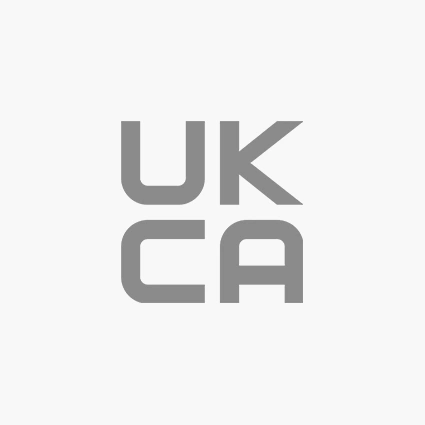
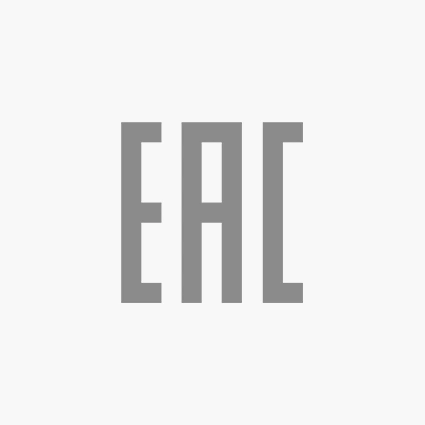
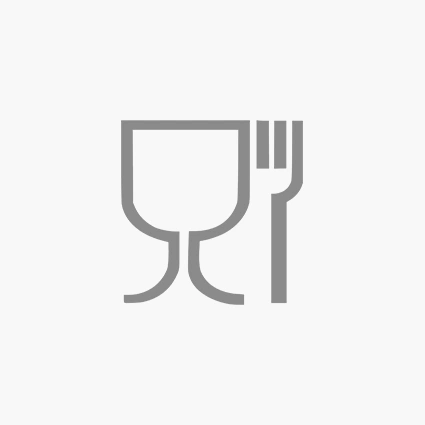
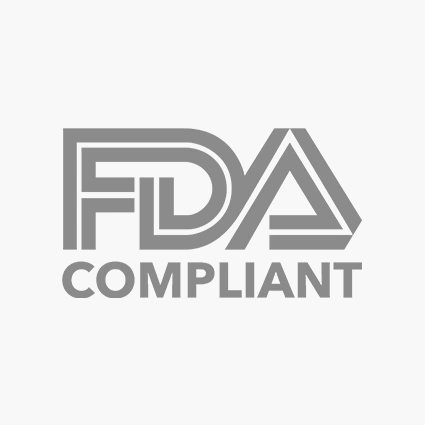
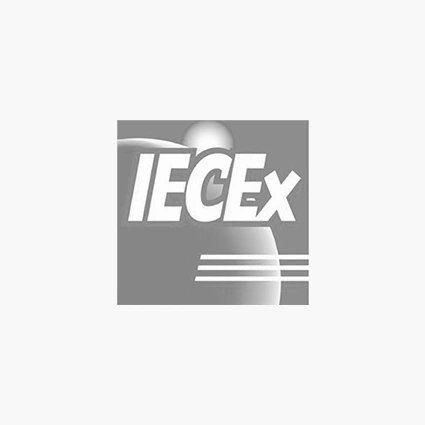