Double diaphragm pumps
Phoenix Range
The Phoenix Range represents an evolution in the field of diaphragm pumps, offering an efficient and reliable means for the transfer of fluids in a variety of industrial applications. These volumetric hydraulic pumps operate through the alternating movement of two opposing diaphragms, moving the fluid from a lower suction manifold through the pump body to a discharge manifold. Their English name, “Air Operated Double Diaphragm” (AODD), emphasizes that the movement of the diaphragms is pneumatically controlled via an air distributor.
This versatile design allows for the management of a wide range of fluids under different viscosity conditions, with exceptional performance. The Phoenix Range pumps can draw liquid from significant depths and pump at high head pressures, making them suitable for multiple industrial applications. With supply pressures ranging from 1.5 bar to 8 bar, these pumps are ideal for working in various environments, ensuring reliable and efficient fluid transfer. The Phoenix Range embodies innovation and excellence in diaphragm pump technology, representing an ideal choice for fluid transfer needs in diverse industrial sectors.
How a Diaphragm Pump Works
A diaphragm pump is a pneumatic hydraulic pump that operates through the movement of two opposing membranes.
Main components include:
- The central body: the ends are the opposing air chambers connected by the pneumatic distributor. Through it, the intake and discharge of compressed air occur;
- The pneumatic distributor is the component that ensures a continuous air exchange in the two opposing chambers, maintaining a nearly 1:1 ratio between the volume of fluid and air. It consists of a movable bushing connected to the shaft that manages the opening and closing of the air passages from one chamber to the other of the spool, all enclosed in a fixed cylindrical body for loading and unloading from the central body. The FLUIMAC distributor allows double diaphragm pumps to be operated with compressed air between 2 bar and 8 bar; It is possible to improve the performance of the diaphragm pump by acting on the number and arrangement of circulation channels and on friction between parts:
– they must ensure a complete load of one chamber and simultaneously the complete discharge of the other, avoiding stall situations where the forces between one membrane and the other balance out,
– if the friction is too high, there is not enough smoothness between the concentric parts, requiring an increase in air pressure and its consumption, making the diaphragm pump start at too “high”pressures.
- The diaphragms are the elastic elements and main components of the diaphragm pump that allow fluid movement. They are made of rubbers that change their properties depending on the environment of use. On one side, they come into contact with the compressed air and on the other with the working fluid. The two diaphragms, being perfectly opposed, perform opposite work during the work cycle: when one inflates, allowing the pumping of the fluid, the other deflates, creating a vacuum in the fluid chamber, thus allowing the suction of the latter. They are designed so that their shape does not interfere with the distributor and to decrease flexural stress or increase thrust force.
From them derives the name double diaphragm pump.
- The pump bodies are the fluid passage chambers of the double diaphragm pneumatic pump. They contain a non-return ball valve in suction and one in discharge that open and close oppositely based on the fluid load or discharge phase. The valves, composed of ball, seat, and cage, are perfectly concentric to the diameter of the suction and discharge channels of the pump body to avoid fluid leakage and ensure the fluid’s passage through the inner diameter. The ball rests completely on the inner circumference to prevent reverse fluid motion, and the cage restricts it to only vertical movement, not transverse. Based on the displacement of the diaphragm pump body, different flow rates can be developed, whereas based on the constituent material (PP, PVDF, POMc, AISI, aluminum, etc.), chemically different liquids are processed;
- The collectors are the fluid passage channels of the double diaphragm pump. We have a suction collector and a discharge collector. They connect the two opposing working chambers. Based on their diameter, different flow rates can be pumped; they are made of the same materials as the pump bodies depending on the type of liquid pumped.
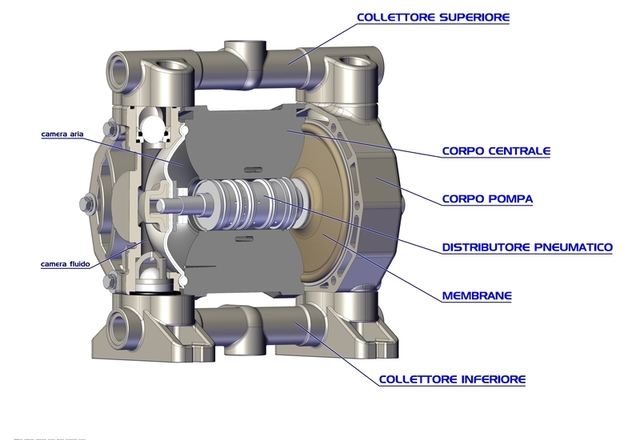
HOW DOES A DIAPHRAGM PUMP WORK?
OPERATING PRINCIPLE OF THE DOUBLE DIAPHRAGM PNEUMATIC PUMP
The diaphragm pump is a volumetric hydraulic pump that processes the working fluid in a control volume that varies periodically over time, with typically non-steady flow. In PHOENIX diaphragm pumps, the fluid travels from the lower suction manifold to the pump body and then to the delivery manifold through the alternating movement of two opposing diaphragms. In English, it is called Air Operated Double Diaphragm AODD because the movement is imparted to the diaphragms pneumatically through a shaft controlled by a distributor, into which compressed air is introduced into a chamber adjacent to the pumping chamber. Thanks to this mechanism, the diaphragm pump can also be called a pneumatic diaphragm pump, or more precisely, a double diaphragm pneumatic pump.
In the double diaphragm pump, the head of the working fluid is high, despite its relatively compact size: if already primed, it can suck liquid from 9 meters and pump up to 9.8 meters high on primed suction. These heights can be limited by the viscosity of the fluid itself, the higher the viscosity, the lower the head.
The supply pressure is instead constrained by the frictions between the components of the distributor and the air passage channels available. The fluid-air ratio is about 1:1. Double diaphragm pneumatic pumps can be made for small and medium flows, and medium and high heads.
Diaphragm pumps typically operate with supply pressures in the range of 1.5 bar to 8 bar.
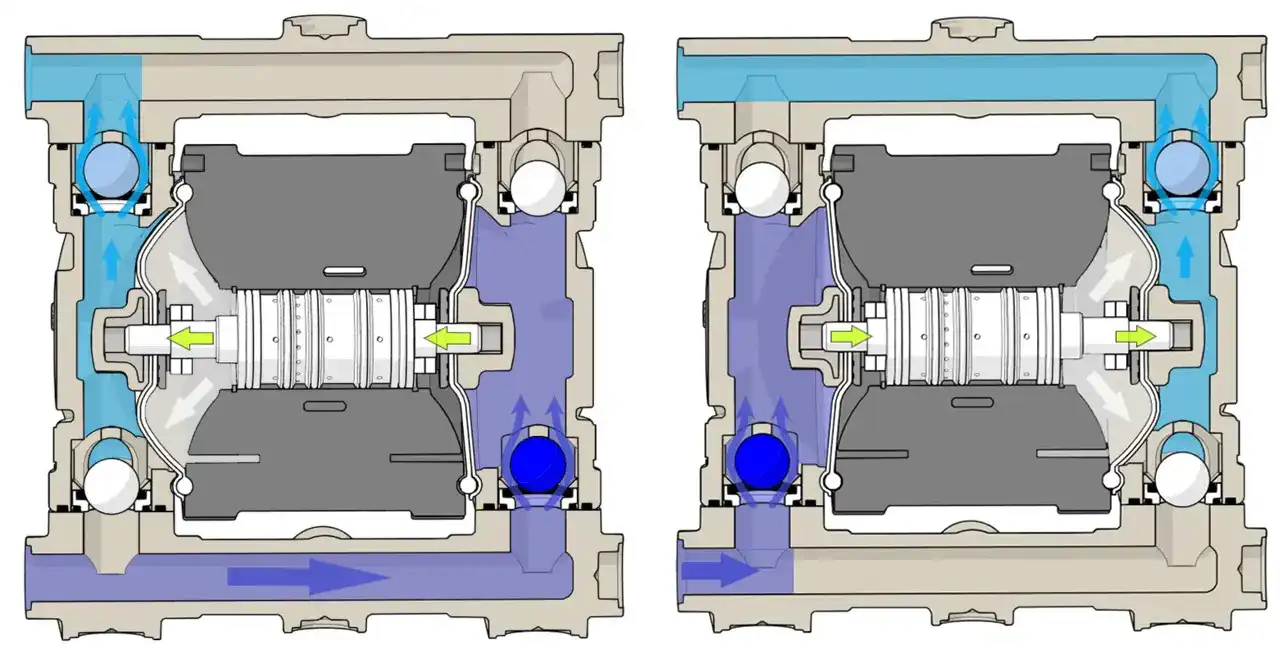
LET'S SEE THE WORKING CYCLE OF A DIAPHRAGM PUMP
Phase 1 air side: The air, through the opening of the distributor channels, passes into the left membrane which inflates. The shaft pulls the right membrane which deflates, conveying the excess air to the discharge.
Phase 1 fluid side: In the left chamber, the fluid is exiting from the delivery manifold under the pressure created by the membrane. The suction ball is closed and the delivery ball is open.
In the right chamber, a vacuum is being created (due to the deflation of the membrane’s air) allowing the opening of the suction ball and the passage of the fluid through the suction manifold. The delivery ball is closed.
Phase 2 air side: Once the left membrane has finished charging, it begins to discharge. Other channels on the distributor then open, directing air into the right membrane which inflates.
Phase 2 fluid side: When the left membrane discharges, the left chamber fills with fluid. The suction ball opens due to the vacuum created, and the fluid passes through the suction manifold. In contrast, in the right chamber, the fluid is pushed into the delivery manifold, the suction ball is closed while the delivery ball is open.
With only two working phases and no idle period, the cycle of the double diaphragm pneumatic pump is complete and can begin again.
ADVANTAGES OF THE DOUBLE DIAPHRAGM PNEUMATIC PUMP
- Does not stall or cavitate: Unlike a centrifugal pump, the pneumatic diaphragm pump can operate at any flow rate without cavitation, and the fluid is not at risk of vaporizing since the pressure in the chamber will never be lower than the fluid’s vapor pressure. Fluimac S.r.l. has long produced double diaphragm pumps and has developed a method to separate the feed from the pump body, making assembly less difficult and reducing the risk of stuck parts, gaskets, and o-rings, while increasing air passage channels reduces the risk of pneumatic pump stalling. Moreover, increasing the number of tightening screws has reduced the risk of pump leaks, providing greater compression to the gaskets;
- Self-priming: Thanks to this feature, the diaphragm pump can suck fluid even if placed above the free surface, even when dry, i.e., without initial liquid, up to 4 meters high. It does not risk temperature increases and/or friction that damage the pump and membranes. If already primed, it can suck liquid from 9 meters and pump up to 9.8 meters high on primed suction;;
- No electricity required: For powering the pneumatic diaphragm pump, an air compression system (range between 1 and 8 bar) is needed, which can sometimes be an advantage due to the absence of electricity near the liquid;
- Capable of processing almost all types of existing fluids: As the diaphragm pump is driven by compressed air, with wider and varied fields and usage pressures, the pumping chambers fill and empty regardless of the worked liquid, moving even very dense or viscous substances. With double diaphragm pumps, it is possible to process highly acidic, corrosive, or alkaline liquids, paints, glues, high viscosity liquids up to 50 CPS, food products, or liquids with solid particles up to 2 mm in diameter in the smaller configurations, and up to 12 mm in the larger ones. Using pneumatic diaphragm pumps for fluids with maximum allowed viscosity leads to a decrease of up to 90% of the nominal flow rate;
- Easily adjustable: It is possible to vary the flow rate easily by decreasing the pneumatic air load at the inlet, or by closing the suction manifold. Thanks to this feature, the PHOENIX double diaphragm pneumatic pump is adaptable to different types of systems: based on the supply pressure, from 2 bars to 8 bars, it is possible to obtain different characteristic curves;
- Adaptable and versatile: based on the application field, it can be modified as needed
- Pump and double diaphragm in different attachment configurations to adapt to any system layout;
- Submersible double diaphragm pumps (useful in draining tanks);
- Accurate double diaphragm pumps (with remote control); double diaphragm in different attachment configurations to adapt to any system layout
- Twin double diaphragm pumps (with separate chambers and manifolds, ability to pump two liquids simultaneously);
- Double diaphragm pumps for hanging or installations on drums and tanks;
- Double diaphragm pumps for installations under hoppers for high viscosity fluids;
- Double diaphragm pumps for food;
- Diaphragm powder pumps (for moving powders);
- Diaphragm pumps installed on trolleys to facilitate transport
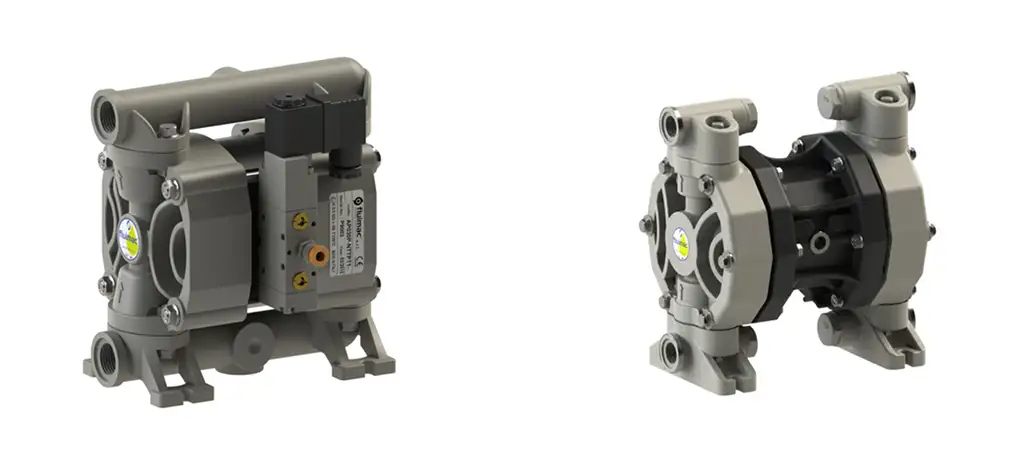
CHOOSING THE MATERIAL OF THE DIAPHRAGM PUMP
Choosing the material for the diaphragm pump is crucial to ensure adequate performance for the system, guarantee safety for operators and the environment, protection of the pump itself, and the chemical and temperature compatibility of the liquid with the construction materials.
The materials differ based on the pump bodies with manifolds, diaphragms, non-return valves with their balls, and gaskets.
- Double diaphragm pump with components in POLYPROPYLENE (PP) for general use, where broad chemical compatibility is required. There is a conductive version for ATEX environments;
- Double diaphragm pump with components in PVDF where high chemical resistance to acids and high temperatures is required. Conductive version for ATEX environments;
- Double diaphragm pump with components in ACETAL (POMC) or ALUMINUM for pumping solvents and hydrocarbons or where good abrasion resistance is required;
- Double diaphragm pump in AISI 316 for excellent corrosion and abrasion resistance, or AISI 316 ELECTROPOLISHED for FOOD applications;
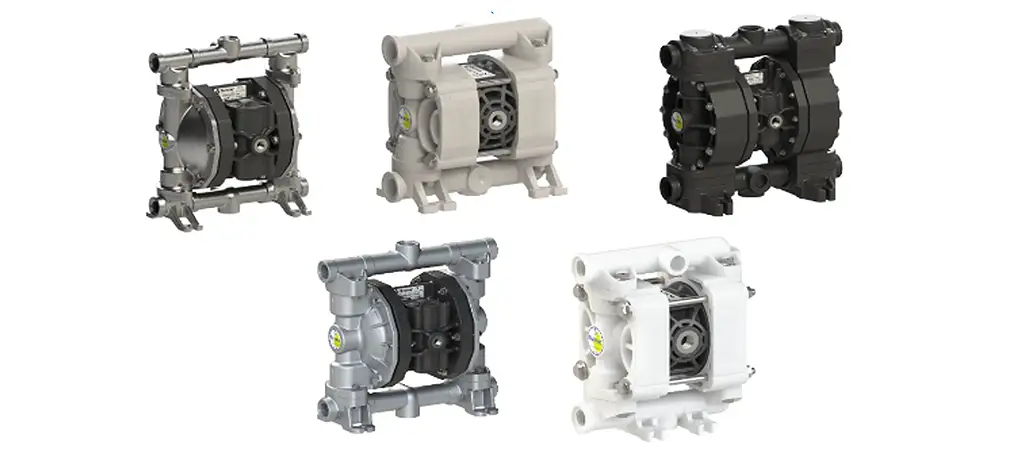
Diaphragms, balls, and gaskets:
- L’NBR is suitable for oil-based fluids, petroleum, water, hydrocarbons, and all mild chemicals. It has fairly common use;
- EPDM for alkaline solutions, diluted acids, ketones, and alcohols, as well as applications with abrasive liquids;
- Il PTFE has broad chemical compatibility as well as high corrosion resistance and non-stick properties. It is well suited for high-temperature applications;
- Diaphragms in HYTREL have good resistance to low temperatures and abrasion. They have fairly common use;
- Diaphragms in SANTOPRENE are ideal for solutions and diluted acids;
- Diaphragms in AISI if excellent abrasion and corrosion resistance is needed or for very viscous liquids;
- Gaskets in VITON have good resistance to heat, aggressive chemical agents, and hydrocarbons. They are among the most used for diaphragm pumps in general applications.
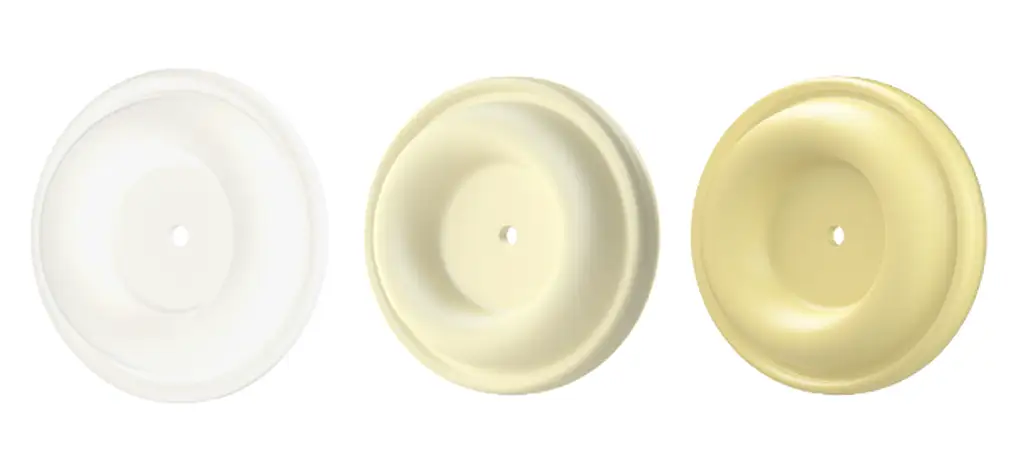
Ask for advice
Do you need support in choosing the centrifugal pump most in line with your specific fluid handling needs?
Fill out the form below and you will be contacted by our staff.
The best solutions, certified
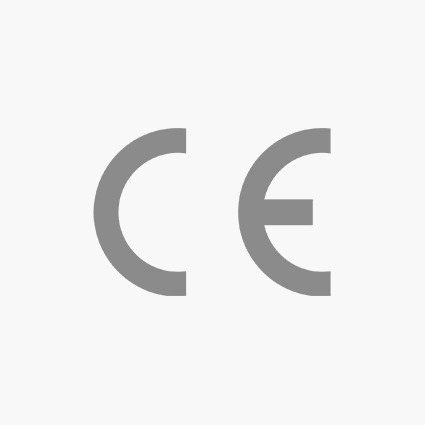
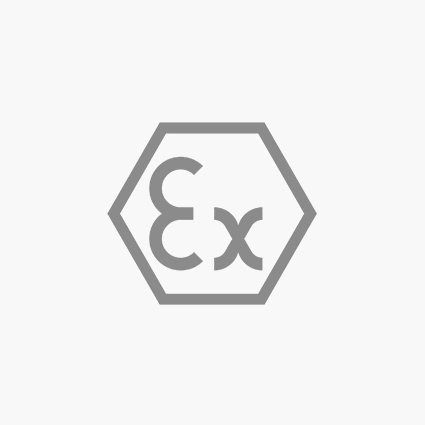
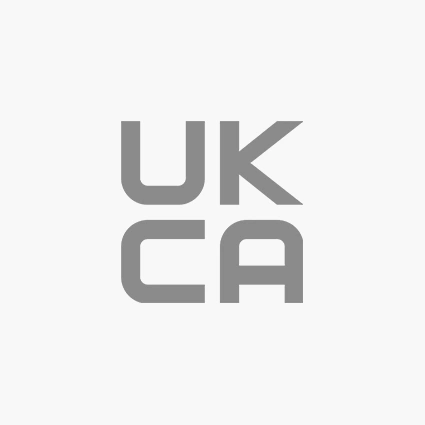
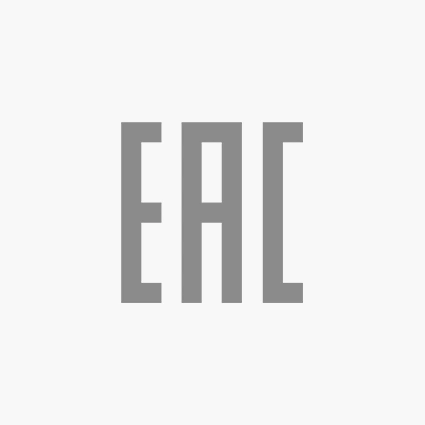
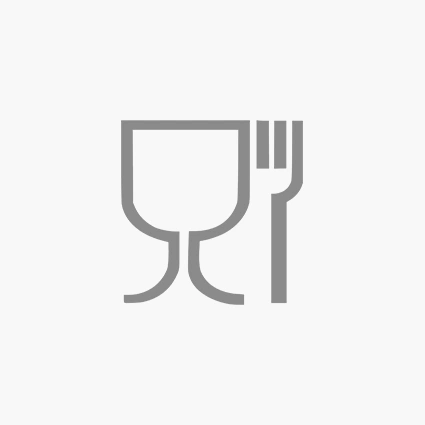
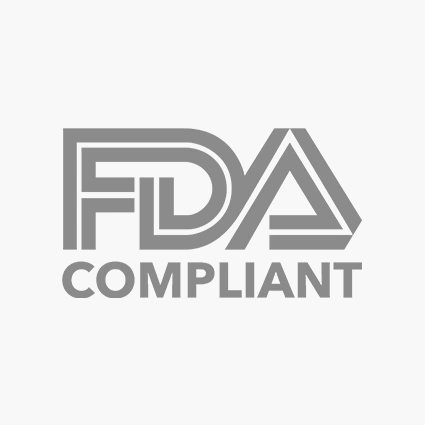
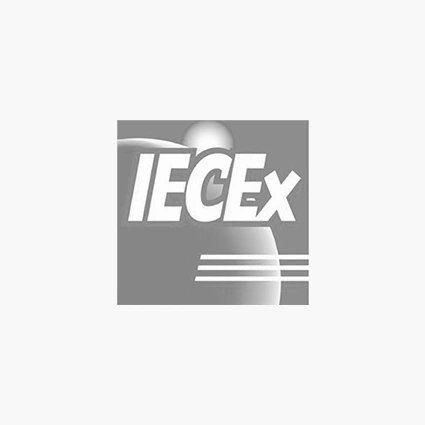